Â
5 Questions With Thomas Thrasher of Suffolk Construction
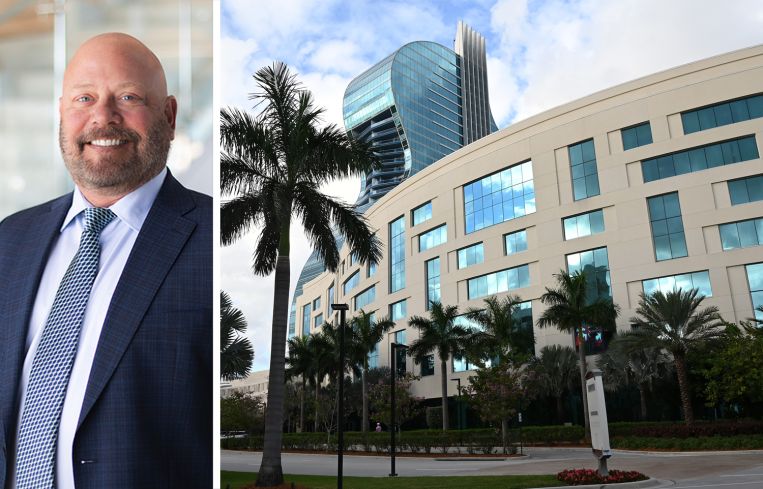
Thomas Thrasher, general manager of Florida East Coast operations for Suffolk, and Seminole Hard Rock Hotel & Casino. PHOTOS: Courtesy Suffolk Construction; Desiree Navarro/Getty Images
South Florida is in a building boom, and Thomas Thrasher is positioned in the middle of the action.
Thrasher is general manager of Florida East Coast operations for Suffolk, one of the largest contractors in Florida. Suffolk’s recent projects include the Seminole Hard Rock Hotel & Casino, Virgin Voyages’ Terminal V, the Make-A-Wish headquarters in Miami and The Bristol condo in West Palm Beach. The company is working on a new command center for Miami-Dade County and a terminal expansion at Palm Beach International Airport.
SEE ALSO: New York-Area CRE Owners Alter What They Traditionally Invest In
The following conversation has been edited for length and clarity.
Commercial Observer: During the pandemic, supply chain disruptions led to soaring costs for building materials. Has that calmed down?
Thomas Thrasher: It has. We are able to plan ahead. There are still a few things that are a challenge. For example, it’s 14 to 16 months to get switch gear – when power comes into the building from FPL to the transformer, the power has to go through a switch gear. The wait has been 14 to 16 months for about two years now.
Labor is another ongoing issue for your industry. What’s happening on that front?
That’s been an issue for as long as I’ve been in construction. How do we battle that issue? One is trying to get more people into the workforce. We have to start early. We get involved with mentorship at the high school level. The second one is tech and innovation. We have our Boost program, which helps us invest in tech and AI to make us more efficient.Â
The construction industry is incredibly inefficient, so we really key in on the things that let us do more with less people. For instance, to do inspections, we can put a camera on a worker’s hard hat. The software takes photos of the site and compares that to the plan. We also have a robotic dog that will walk around the site after hours and take pictures for us of certain things.
Have you been able to add enough automation to make a dent in the labor shortage?
It is making a dent on our larger projects. We can measure the number of labor hours we’re saving. But if you think about construction, it’s still so labor intensive. You have to lay bricks. You have to pour concrete.
How have the rules put in place following the Surfside condo collapse affected you?
I think in a good way. It was not a bad knee-jerk reaction; it was a good knee-jerk reaction. From a structural standpoint, not everything was being looked at. We build some complex buildings, so we have a lot of quality control. Maybe not every other building had that.Â
But from our standpoint, everything we build is code or code-plus. The weather conditions in Florida are tough. Just about every building has rebar. We’ve started using epoxy-coated rebar, or maybe setting the rebar farther back from the face so it’s not as susceptible to water damage. And when we build buildings, we don’t just walk away. We go back once a year and make sure the managers are maintaining the buildings.
What’s your biggest challenge?
Interest rates. When you’re building condos or apartment buildings, the developers are out looking for loans. It’s been a little bit slow, because the cost of construction went up, the cost of land went up, and the cost of capital went up.
Jeff Ostrowski can be reached at jostrowski@commercialobserver.com.
  Â